The impact of continuous improvement
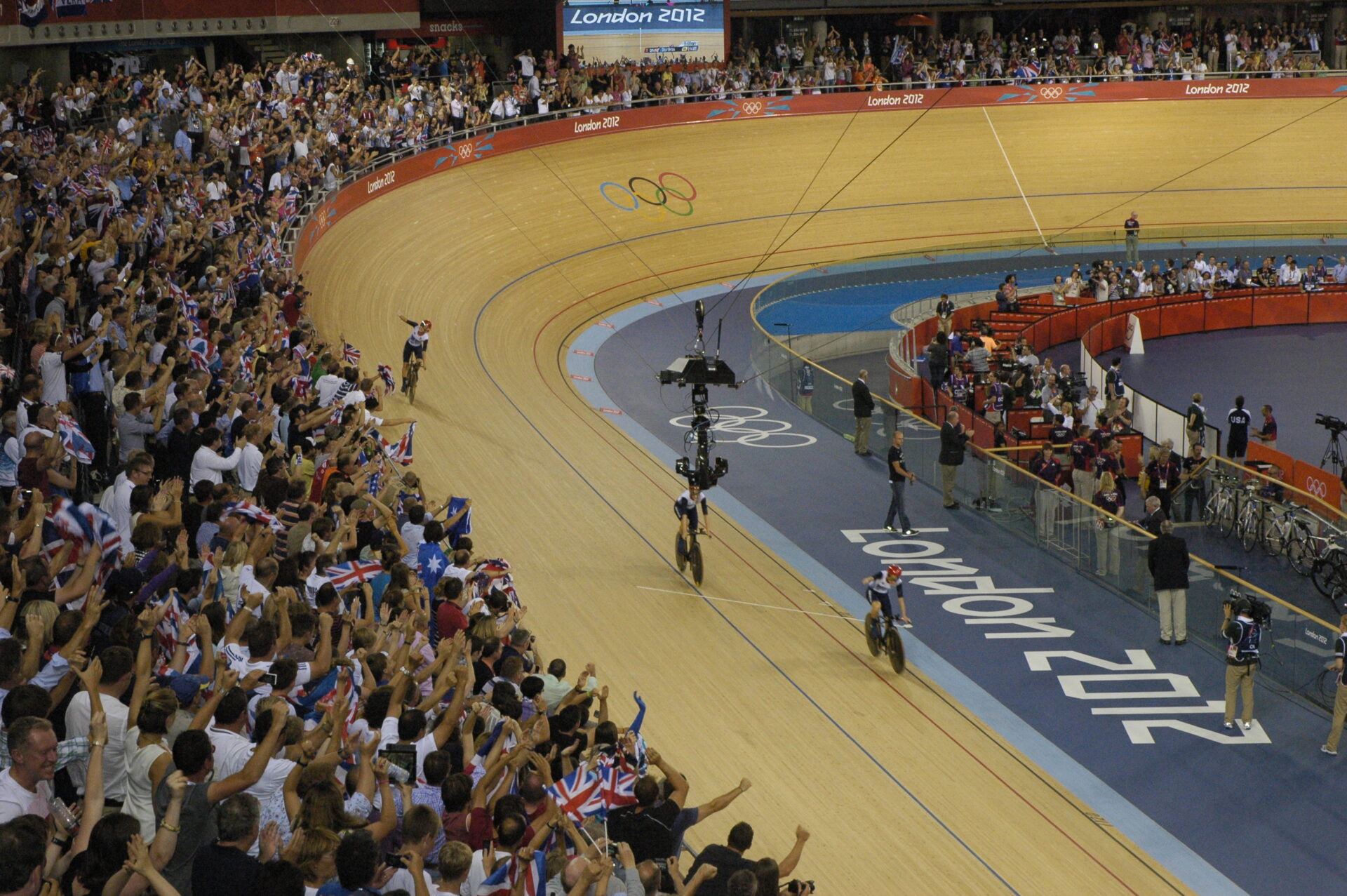
In 2002, the British Cycling Team hired a new Performance Director, Dave Brailsford, to turn around the team’s poor performance. Their lack of wins had resulted in top bike manufacturers in Europe refusing to sell bikes to the team because they feared it would hurt sales if other professionals saw the British team using their gear.
Brailsford, who holds an MBA, applied the continuous improvement theory of marginal gains to the team. He led the team to break down everything that goes into competing and then improve each element by 1%. Thus, they would achieve a significant aggregated increase in performance.
‘Brailsford and his team continued to find 1 percent improvements in overlooked and unexpected areas. They tested different types of massage gels to see which one led to the fastest muscle recovery. They hired a surgeon to teach each rider the best way to wash their hands to reduce the chances of catching a cold. They determined the type of pillow and mattress that led to the best night’s sleep for each rider. They even painted the inside of the team truck white, which helped them spot little bits of dust that would normally slip by unnoticed but could degrade the performance of the finely tuned bikes.
Just five years after Brailsford took over, the British Cycling team dominated the road and track cycling events at the 2008 Olympic Games in Beijing, where they won an astounding 60 percent of the gold medals available. Four years later, when the Olympic Games came to London, the Brits raised the bar as they set nine Olympic records and seven world records.’
Excerpt from Atomic Habits, written by James Clear
‘The 1 percent margin for improvement in everything you do.’ – Dave Brailsford
This is a great example of how even a 1% margin of continuous improvement can have a monumental impact.
While tackling improvements can seem like an overwhelming and large activity that may require expensive technology, the example above shows that it doesn’t have to be. Continuous improvement can be the simplest, smallest change that results in more efficiency, less waste, more effective use of resources and improved outcomes.
This philosophy, known as ‘Kaizen’, comes from Japanese words meaning change for the better or improvement. Within the business context, improvement became continuous improvement. Kaizen is continuous improvement involving everyone, from the CEO to the assembly line workers. Like the British Cycling team, taking a holistic approach can highlight how much we can improve.
A continuous improvement plan is a method of standardising improvement throughout the organisation. Continuous improvement works best when it becomes a mindset and is ingrained in the key processes and practices of the organisation.
Developing a continuous improvement plan can include:
- Documenting areas for improvement.
- Identifying gaps in systems and processes that do not meet standards.
- Outlying planned actions/tasks to be undertaken.
- Allocating responsibility for improvement activities to relevant people in your organisation.
The Parbery Business Performance Improvement team can help you on your continuous improvement journey by identifying and documenting your current practices in collaboration with you to understand what works well, what 1% looks like for you, and how we can help you make the 1% count.
By Alissa Addicks, Senior Manager